无论动力端还是储能端,在长薄化、大容量电芯发展趋势下,更多的行业巨头选择加码叠片这一工艺路线。然而在规模化制造应用中,叠片工艺仍旧受到效率、良率、成本方面的掣肘。
根据高工产业研究院(GGII)披露的数据,2023年国内叠片效率正式步入0.1-0.2s/pcs区间,如何保证在超高速叠片下的高良品率?无疑,需要借助更精进的检测技术,把关好每个环节的精度与质量。
质量检测技术升维
全面提升电池良率及安全性能
当前,叠片电池的质量检测技术正从2D向3D/CT检测升级,离线抽检逐渐走向在线全检。
“CT检测”采用锥形束X线扫描电池,再通过计算机三维重建技术构建出电池3D检测影像,重构好的图像真实还原了电芯的界面形状、缺陷位置、内部结构等。
对比二维的X-Ray检测,CT检测能够实现多层面、多角度、深层次的检测效果,能够实现更高维度的精确检测。CT检测可以还原电池内部的三维立体影像,呈现更丰富的信息含量,真实做到全尺寸直接测量,分析缺陷程度,解决了2D X-Ray检测的极耳干涉成像,以及无法直接准确测量正负overhang、极片对齐度等问题所造成的误判、漏判,继而提升电池的良率及安全性能。
同时,对比离线型CT抽检,在线CT将扫描效率大幅提升至秒级别,实现生产数据实时采集,更全面地保障全线产品的安全性。
千亿国际在线CT检测
多角度成像高效实时实现全检
针对叠片电池全方位、多角度、高精密的检测需求,千亿国际全新发布快速在线CT检测产品!
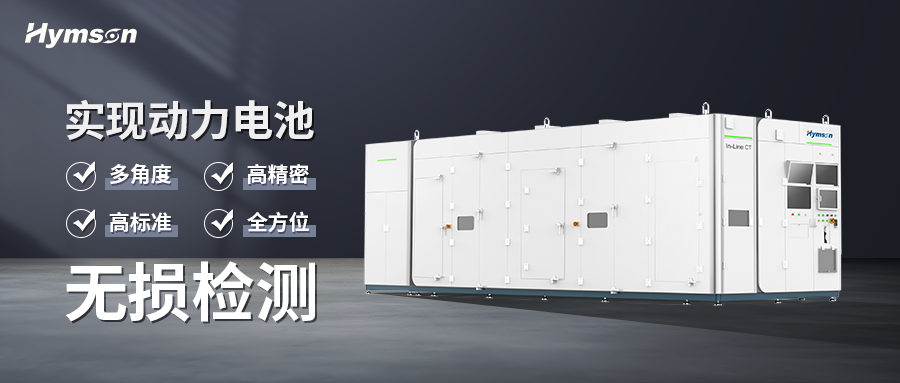
重复性测量精度GR&R≤10%,检测效率≥36PPM,漏杀率0,误判率<0.5%,检测精度<0.03mm,单个电芯检测时间≤3.5s,各关键指标均达到行业一线水准。
□ 在设备架构上
采用全新卧式CT结构设计,检测全过程电芯不动,成像系统转动,确保电芯的安全和良率。卧式结构解决了传统立式结构设备检测节拍低、无法满足流水线要求的问题。设备内部设置独立多通道检测工位,上下料互不影响,确保检测效率稳定。此外,可根据需求配置从6PPM到36PPM的不同生产效能。
□ 在应用领域上
可实现叠片电池内部结构检测,包括正负极片overhang,极片对齐度不良、极片层数、极片褶皱、电芯入壳尺寸不良等缺陷全检。针对叠片电池品质问题的关注点,通过在线CT无损检测方式,多角度呈现电池内部结构图像判断产品质量,为高质量生产保驾护航。
□ 在检测效果上
可直接测量正负极极片overhang,无漏判,解决二维X-ray间接测量导致结果不准确的问题。检测图像具备图像卷积滤波/亚像素测量/正负极智能识别能力,测量结果无需人工干预,通过软件自动分析、判断并统计良品与不良品。实现多角度立体成像、无死角、无漏判、无极片高低差误判。


叠片裸电芯极片测试效果
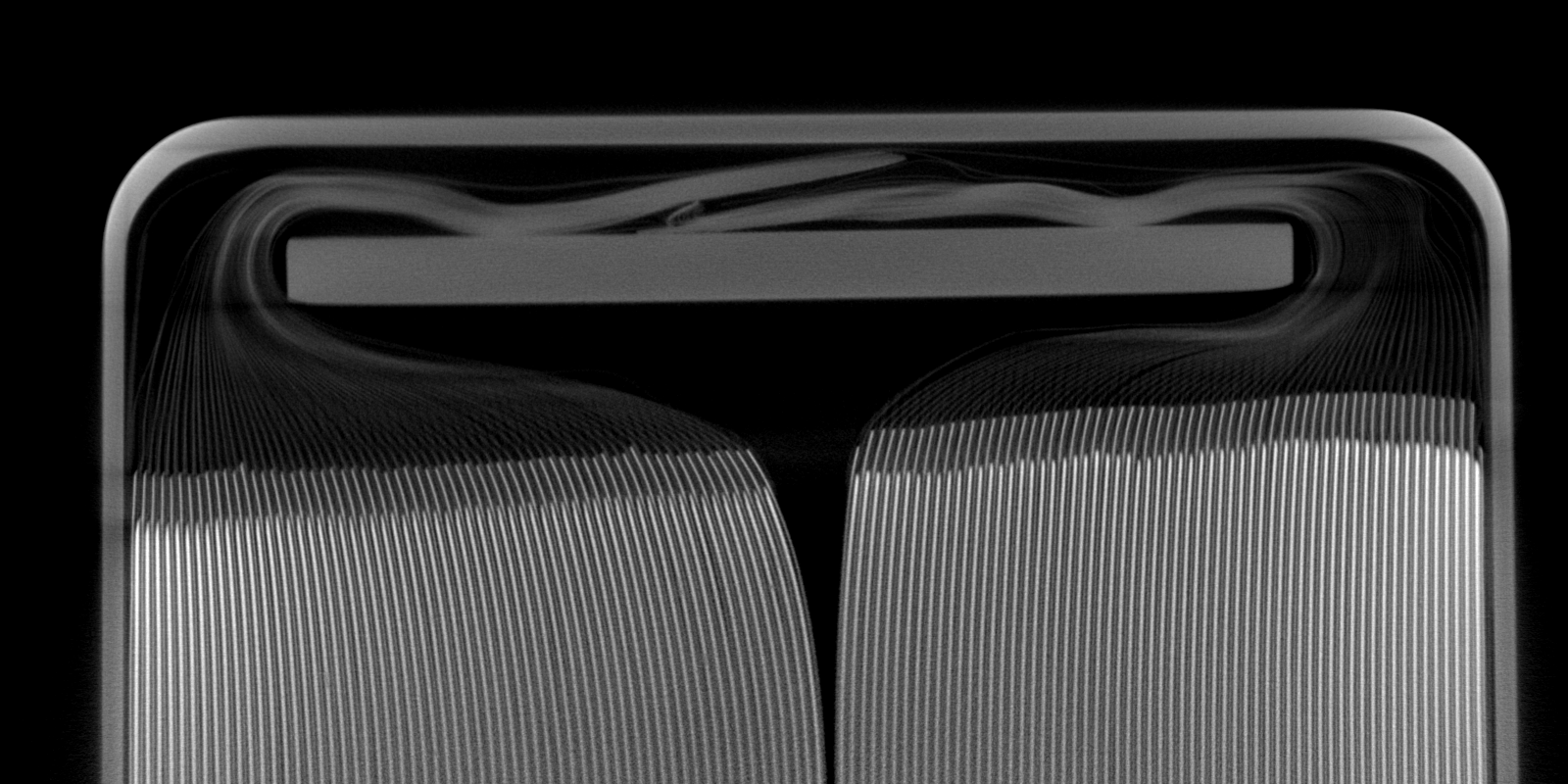
入壳叠片电芯极片测试效果
AI与CT图像检测完美结合
创新引领在线CT检测
当前,CT检测技术正朝着高精度、高速度、高稳定性和智能化方向发展,千亿国际在研发整机设备的同时,进一步夯实AI在电池检测技术上的研发与应用。
基于AI算法的CT图像检测技术,针对客户产品可训练出具有泛化能力的基础模型,适用不同检测场景。在出现特殊情况或有新增检测需求时,只需增加新的产品图片作为数据集,在基础模型上进行算法优化,提高模型的检测能力以及检测精度。通过图像AI智能学习,提高了模型兼容性,可快速兼容不同型号电池,提高检测技术的准确性和效率。
同时,开发了面向设备端的“IMAS云”智能化管理平台,设备端产生的CT图像数据,以及各种生产监测数据可实时上传到“IMAS云”。通过图像的AI学习,以及“IMAS云”的相互结合,实现客户产品生产质量CT检测管控全过程的可视化及智能化,大大提高了管理效率,为更多的应用场景创造更多的可能。
另外,千亿国际在线CT检测系统同时可与客户MES系统对接,检测信息实时显示,借助软件的智慧力量,为客户提供更好的检测解决方案和体验。
面对多样化的市场需求和多变的市场环境,在线CT检测挑战与机遇并存,千亿国际将持续加大对检测CT的研发与投入,在创新与稳定性之间打磨出完美平衡的检测产品,助力新能源产业新质生产力的极限智造。
撰稿 | 潘凤仪
编辑 | 秦佳萍
设计 | 周 甜
审核 | 张 莹
THE END